Chemical Composition and Pozzolanic Requirements
Introduction
As the concrete industry seeks low-carbon alternatives to traditional cement components, natural pozzolans are gaining renewed attention—especially in regions facing fly ash shortages. Among these, diatomite, a siliceous sedimentary rock formed from fossilized diatoms, offers a promising path forward. Thanks to its high amorphous silica content and favorable reactivity, diatomite can serve as an effective supplementary cementitious material (SCM). Understanding diatomite pozzolan chemical composition is essential for evaluating its suitability in concrete applications. This article examines diatomite’s chemical and mineralogical characteristics, its performance as a pozzolan, and its growing potential as a sustainable solution in modern cement and concrete production.
Chemical Composition and Pozzolanic Requirements
Diatomite (diatomaceous earth) is a siliceous sedimentary rock composed largely of silica (SiO₂) with minor impurities. High silica content is critical for pozzolanic activity – typical oven-dried diatomite contains about 80–90% SiO₂, along with 2–10% Al₂O₃ (often from clay) and 0.5–2% Fe₂O₃. The silica is largely in an amorphous (non-crystalline) form, which is reactive with lime. In contrast, any crystalline quartz present is much less reactive at ambient temperature. Pozzolanic quality is usually indicated by a high total of SiO₂ + Al₂O₃ + Fe₂O₃ – ASTM C618 (Class N) specifies a minimum of 70% for this sum. Diatomite deposits often meet this, given their high silica content (e.g. global diatomites range 70–90% SiO₂). ASTM C618 also limits undesirable components: for example, loss on ignition (LOI) (indicating moisture or organics) is typically required to be below about 10%. Raw diatomite can have LOI in the high single digits due to 2–8% “combined water” in the opaline silica and any organic matter. Calcining the diatomite or thorough drying reduces LOI and increases the effective SiO₂ percentage (one test showed ~8% LOI which, when removed, raised SiO₂ from ~85% to ~89%). Generally, a low-calcium composition is preferred – diatomite naturally has very little CaO (often <1%), aligning it with low-Ca Class F fly ash in chemistry. In summary, optimal pozzolan-grade diatomite is high in amorphous SiO₂ (often >80%), has moderate alumina (2–8%) and minimal lime or organics (meeting ASTM chemical criteria for natural pozzolans).
Mineralogical Characteristics (Amorphous vs. Crystalline)
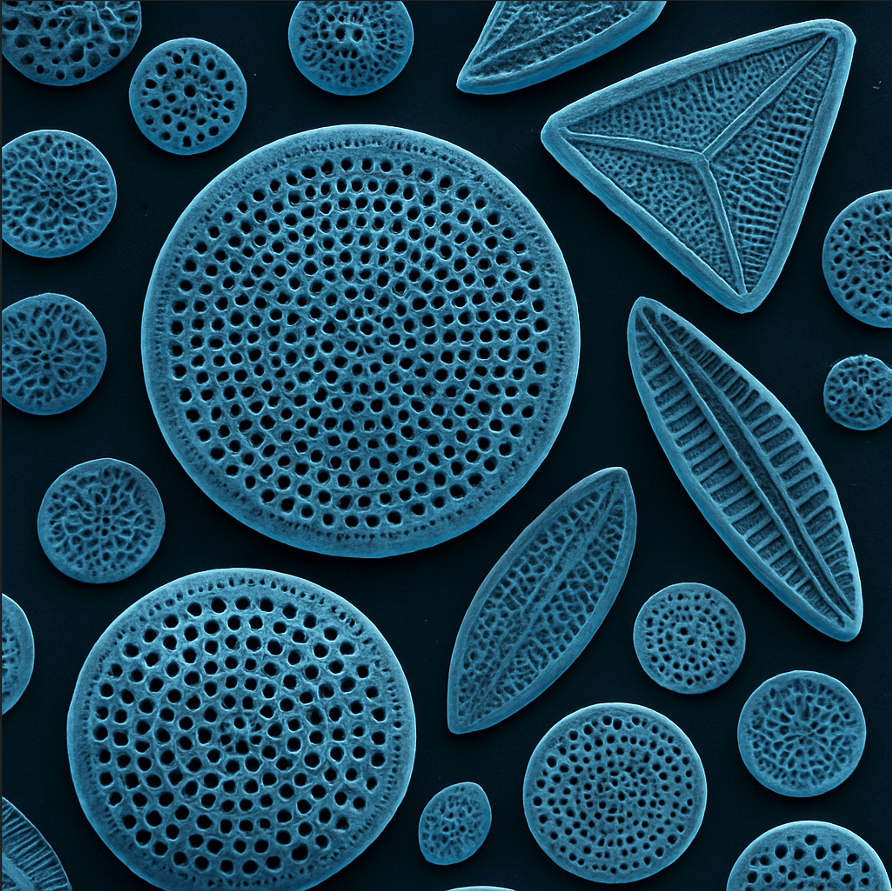
Diatomite’s pozzolanic behavior stems from its mineralogy: it consists of the microscopic frustules of diatoms (algae) which are made of opaline silica. This opal-A silica is an amorphous phase, giving diatomite its high reactivity. A typical diatomite is “mainly amorphous silica with minor amounts of alumina and ferric oxide,” and only minor crystalline minerals (such as residual quartz, clays like muscovite/illite, or feldspars). X-ray diffraction patterns of raw diatomite show a broad hump (amorphous silica) rather than sharp crystalline peaks. The amorphous fraction is crucial – studies note that total chemical composition alone “does not say anything about reactivity… it is essential to know the content of reactive amorphous phases”. High amorphous content correlates with better pozzolanic activity, as these phases readily react with Ca(OH)₂. In one analysis of three diatomite samples, the one with the highest amorphous content exhibited the greatest lime reaction, whereas samples with more crystalline silica or clay showed lower reactivity【12†L27-L35**]. Thus, diatomite is valued as a pozzolan when it retains a high proportion of non-crystalline silica. Minor crystalline content (e.g. small quartz or clay inclusions) is common【41†L590-L599】 but generally these act as inert fillers rather than reactive components. By contrast, excessive crystallinity (for example, diatomite diagenetically altered to hard chert or containing cristobalite after overheating) would reduce pozzolanic performance.
Physical Properties (Fineness, Surface Area, Density)
Particle fineness and surface area are key to how well diatomite behaves in cement. Natural diatomite is extremely porous and lightweight – it has been described as “chalk-like, very fine-grained… very low in density (floating on water until saturated)”. The frustule particles have a highly intricate, porous structure with up to 80–90% voids by volume. This yields an enormous specific surface area: diatomite powders can have BET surface areas on the order of 100–200 m²/g (far higher than typical cement or fly ash). Such high surface area can enhance pozzolanic reactivity (more area for reaction) but also increases water demand in concrete (due to absorption in pores). To be used as a cementitious admixture, diatomite is usually ground to a fine powder – ASTM C618 requires a fineness similar to cement (e.g. at least ~66% passing the 45 μm sieve). Many raw diatomites are soft and friable, facilitating grinding. Once ground, diatomite’s Blaine fineness can exceed that of Portland cement by several-fold. For example, one study found ground diatomaceous earth had a Blaine surface 2–5 times higher than a reference cement. The median particle size of processed diatomite pozzolan is on the order of tens of microns (20–40 μm), comparable to or slightly finer than cement particles.
The density of diatomite also differs from cement. The actual solid (particle) specific gravity of diatomite is around 2.2–2.4, due to its silica composition (lower than Portland cement ~3.15). Its bulk density is much lower (raw fluffy diatomite might be ~0.2–0.4 g/cc) because of the high porosity. In concrete mix design, the lower specific gravity means a given mass of diatomite occupies more volume; proportioning by weight thus increases paste volume slightly, which can affect workability. Workability is somewhat reduced by diatomite addition – the fine porous particles tend to absorb mix water and can make the fresh concrete mix less fluid if water is not adjusted. However, researchers report only a slight slump reduction at 10–15% replacement levels when proper admixtures or water adjustments are used. Overall, achieving sufficient fineness (often by milling) is critical: fine particle size maximizes the pozzolanic reaction rate and strength contribution of diatomite, while the inherently high surface area aids in pozzolanic activity (at the expense of greater water demand which may require plasticizers).
Performance in Concrete (Strength, Durability, ASR Mitigation)
When used appropriately, diatomite as a supplementary cementitious material can enhance concrete performance in multiple ways:
- Strength Development: Diatomite typically contributes to long-term strength through secondary calcium silicate hydrate (C-S-H) formation. Replacement of cement by diatomite often causes a slight reduction in early (7-day) strength (common with pozzolans due to slower reaction), but strengths at 28 days and beyond can equal or exceed the control if the diatomite is reactive. The optimum replacement level is usually in the 10–20% range by mass of cement. For example, one study found the highest 28-day compressive strength at 20% replacement, reaching ~36.6 MPa which was higher than the pure-cement control. Similarly, other research has noted that about 10% replacement yields maximum long-term strength gain. At these moderate dosages, the pozzolanic reaction of diatomite consumes excess Ca(OH)₂ and densifies the paste, leading to improved later-age strength.
- Sulfate Resistance: Pozzolanic diatomite can improve sulfate resistance of concrete. By binding calcium hydroxide and reducing the permeability of the cement paste, the formation of sulfate-attack-prone phases (like ettringite/thaumasite) is limited. The addition of natural pozzolan (Class N, including diatomite) has been noted to “increase resistance to sulfate attack” in concrete. This is in line with other SCMs (e.g. fly ash, slag) which are known to enhance sulfate resistance when used to replace a portion of high-C₃A Portland cement. Diatomite’s high silica and low calcium content make it similar to a Class F fly ash in this context, effectively diluting and improving the cement matrix against sulfate ingress.
- Alkali-Silica Reaction (ASR) Mitigation: Diatomite is particularly effective in mitigating ASR, which is the deleterious reaction between alkalis in cement and reactive silica in certain aggregates. Paradoxically, while diatomite itself is a form of silica, when finely dispersed in the cement paste it reacts pozzolanically with alkalis and Ca(OH)₂, scavenging alkalis and preventing them from attacking aggregate silica. The use of pozzolans like diatomite “controls the deleterious effects of Alkali Silica Reactivity (ASR)” by reducing available alkali hydroxides and by consuming them in secondary C-S-H. Field experience supports this: a natural pozzolan blend of diatomite/ash from California (marketed as Lassenite) has been shown to mitigate ASR expansion in concrete containing reactive aggregates. Laboratory tests on a Nevada diatomite/pumice pozzolan also found it “exceeds ASTM C618 specifications and mitigates deleterious ASR”. In practice, structures that incorporated diatomaceous pozzolan (e.g. the Palo Verde Nuclear Station concrete) have shown durable performance in part due to ASR control.
- Other Durability Factors: The fine particle packing and additional C-S-H from diatomite generally decrease concrete permeability, which improves resistance to water ingress, chloride penetration, and freeze-thaw damage. By “decreasing permeability and lowering the heat of hydration”, pozzolans (including diatomite) help produce more durable, mass concrete with reduced thermal cracking tendency. Some studies also indicate diatomite-blended concretes have improved chloride ion resistance and reduced sorptivity (capillary absorption) due to pore refinement. In terms of temperature, diatomite’s effect is similar to other pozzolans: it moderates the early heat evolution from cement hydration (helpful in large pours). Its inclusion has additionally been cited to increase density of the hardened concrete and even offer slight improvements in abrasion resistance (owing to the hard silica micro-particles). Overall, diatomite can contribute to a more durable concrete matrix when properly used.
Raw vs. Calcined Diatomite – Processing Considerations
Most natural pozzolans require some processing, and diatomite is no exception. The two main treatments are grinding (to increase fineness) and calcination (heat treatment to enhance reactivity). Grinding is universally done to achieve the desired fineness (usually to cement-like particle size or finer). Calcination, however, depends on the nature of the diatomite deposit: many diatomites are already amorphous and reactive in raw form, but some benefit from heating to remove impurities or structural water. Key points include:
- Removal of Moisture and Organics: Raw diatomite can contain organic matter and chemically bound water. Gentle calcination (~ >600 °C) burns off organics and removes the 2–8% water associated with opaline silica. This increases the active silica proportion and helps meet LOI limits. For instance, the Long Valley, CA diatomite pozzolan was mined and then ground and calcined to meet ASTM specs as a “high-grade natural pozzolan”. Without calcination, that material’s LOI and reactivity would have been lower. Many commercial filter-grade diatomites are similarly calcined (sometimes flux-calcined with additives) to stabilize their structure; those calcined powders could potentially serve as pozzolan if of suitable chemistry.
- Phase Transformations: Care must be taken with calcination temperature and time. Moderate heating (~500–800 °C) can increase reactivity (by driving off water and perhaps increasing surface area). However, over-calcination (>800 °C) can cause amorphous silica to start crystallizing into cristobalite or tridymite (forms of crystalline silica). These high-temperature phases are less reactive (and cristobalite also poses potential health hazards if abundant). A study on diatomite found that a sample processed only by mechanical means retained more natural opal-A (amorphous), whereas samples that were calcined showed a cristobalite presence – indicating they had been heated enough to “anneal” some silica into crystalline form. Thus, while thermal activation can improve a diatomite’s pozzolanic activity up to a point (and is often needed for high-clay diatomites, analogous to calcining clay to make metakaolin), the process must be controlled. In some cases, natural raw diatomite (especially if very pure and amorphous) is sufficiently reactive without calcination – only drying and grinding may be employed. In other cases (e.g. lacustrine deposits with clay or organic contamination), light calcination is used to achieve consistency and high reactivity.
- Grinding and Blending: After any heat treatment, diatomite is milled to a fine powder. Its softness (Mohs ~1) means energy requirements for grinding are relatively low (much easier than grinding sand or slag). Some commercial natural pozzolan products blend diatomite with other volcanic ash or pumicite to balance chemical and physical properties. For example, a “diatomite+tuff” blend might offer both high amorphous silica and sufficient alumina for strength development. Blended cements (ASTM C595 Type IP) in the U.S. have included calcined diatomaceous earth as part of the pozzolan component in the past.
In summary, raw vs. calcined use depends on the deposit quality: high-purity freshwater diatomite with minimal impurities can be used in raw form (just ground), whereas lower-grade diatomite may require calcining to meet performance criteria. The prevailing practice is to ensure the material meets ASTM C618 Class N requirements through whichever processing steps are necessary – often a combination of drying, milling, and possibly mild calcination.
U.S. Sources and Commercial Use of Diatomite Pozzolans
The United States is rich in diatomite deposits, especially in the West. Major diatomite-producing states include California, Nevada, Oregon, and Washington, largely from extensive Miocene-age lake bed and marine deposits. California alone hosts some of the largest deposits – notably the marine diatomite at Lompoc (Santa Barbara Co.), and extensive freshwater diatomites in areas like Mono and Lassen Counties. While much of the domestic diatomite (≈800,000+ tons/year) is used for filtration, fillers, and other industries, certain deposits have been or are being used as natural pozzolans:
- Lassen County, CA (Long Valley Lassenite): The Long Valley deposit is a lacustrine diatomaceous earth interbedded with volcanic tuff. It was mined intermittently from the 1960s–1980s and the product (trade-named Lassenite) was used as a natural pozzolan in concrete. Notably, Lassenite pozzolan was used in large projects such as Bullards Bar Dam (CA) and the Palo Verde Nuclear Generating Station (AZ) to improve concrete durability. Recent efforts have been made to re-commercialize this resource: as of 2023, PozzSource (a company) secured permits to produce Lassenite natural pozzolan, highlighting its “extremely high pozzolanic activity and ASR mitigation” characteristics. The Long Valley material is a proven Class N pozzolan when properly processed (ground & lightly calcined).
- Nevada and Western States: Nevada hosts several diatomite deposits being evaluated for pozzolan use. For instance, the Hazen deposit in Churchill County is actually a glassy pumiceous material but near diatomite operations, and it has been shown to meet ASTM specs for use in cement. There are also projects targeting pure diatomite deposits (e.g. near Tonopah, NV) for development as pozzolan sources. In Oregon and Washington, diatomite occurrences exist (e.g. in central Oregon) but historically these were used for diatomaceous earth products; their use as pozzolan would depend on local demand and competition from volcanic ash pozzolans in the region.
- High-Purity vs. Pozzolan Use: A crucial commercial consideration is that the highest-purity diatomites (with >90% silica, often marine deposits) have lucrative markets in filtration, fillers, cosmetics, etc. These products can sell for $250–$500 per ton, far above what the cement industry can typically pay. As a result, such deposits are usually not dedicated to pozzolan use. Instead, pozzolan-grade diatomite tends to come from large, lower-cost deposits that may contain some impurities (clays, volcanic ash, etc.) but are still sufficiently reactive. The Long Valley/Lassenite deposit is a prime example: it has both diatomite and volcanic ash (which together provide a good SiO₂-Al₂O₃ blend) and exists in great quantity (estimated over 1 billion tons). Because the material is not as highly valued for filtration (due to being “impure” diatomite), it can be economically used for cement admixture.
- Modern Usage and Logistics: With the decline of coal fly ash availability in some regions, natural pozzolans like diatomite are regaining attention. Transportation is a key factor – pozzolan sources need to be within economical range of cement plants or concrete markets. Many western deposits are advantageously near rail lines or power plants. For example, the proposed revival of the Long Valley pozzolan targets markets in Reno, NV, and Northern California which are reachable by rail/truck. Similarly, if diatomite pozzolan is produced in Nevada or Eastern California, it can supply the Southwest and West Coast markets where demand for SCMs is high (and local fly ash is scarce). Some companies also look at blended products (diatomite plus perlite or pumice from nearby sites) to tailor reactivity and optimize logistics by co-locating mining and processing (e.g. the CS Pozzolan project in Nevada integrates a perlite expansion with pozzolan grinding).
- Alternate Sources (Recycled Diatomite): An interesting sustainable angle is the use of spent diatomaceous earth from industrial filtration as a pozzolan. After serving as a filter medium (for beer, wine, swimming pools, etc.), waste diatomite often goes to landfills. Research has shown that this spent DE, which is essentially calcined diatomite loaded with organic residues (burnt off during use), still has pozzolanic properties. One study demonstrated that replacing a portion of cement with spent diatomite powder can increase 90-day strength by ~13% and significantly improve concrete sustainability. Some cement plants have even tested using spent filter cake as a raw feed or additive. Though not yet widespread, it exemplifies how diatomite’s cementitious value can be reclaimed from waste streams.
In conclusion, diatomite’s combination of chemical makeup (high amorphous silica, adequate alumina, low lime), mineral structure (highly porous amorphous frustules), and physical traits (fineness and huge surface area when ground) make it an effective natural pozzolan. It can improve strength (especially long-term), refine durability (sulfate and ASR resistance, lower permeability), and serve as a partial cement replacement to reduce CO₂ footprint. To maximize these benefits, processing like grinding (and sometimes mild calcining) is applied. In the U.S., substantial diatomite resources exist – particularly in the West – and while historically underutilized in favor of industrial byproduct SCMs, they are gaining renewed interest as commercial pozzolan sources for the concrete industry. With proper characterization (per ASTM C618) and logistics management, diatomite is poised to be an important component of sustainable cement and concrete formulations in the region.
Sources: U.S. Geological Survey reports and data on diatomite; ASTM C618 standard specifications; academic studies on diatomite’s properties and performance; industry and government reports on natural pozzolan use (Long Valley Lassenite); and commercial disclosures from pozzolan developers, among others. Each provides insight into the required chemistry, structure, processing, and successful application of diatomite as a natural pozzolan in U.S. cement and concrete.
Interested in exploring natural pozzolan sources like diatomite?
Contact us today to learn how our expert team can assist with mineral exploration, sampling, and resource evaluation for your next project.